Any operator of iron or steel industrial equipment knows they may have to deal with rust; whilst it's not too much of a problem when it happens to hand tools or small metal items, do you know how to get rid of the rust when it comes to large machinery?
What is rust, and what metals are affected?
There's a misplaced myth that all metals rust; that's not correct. Whilst most metals may corrode over time through a process called oxidation, only metals that contain any form of iron - wrought or cast iron - and steel - carbon and even stainless steel - actually rust. Metals like copper, aluminium or lead, which are non-ferrous, have greenish-blue colour corrosion if not kept clean.
So, what is rust? Well, it is an iron oxide that occurs when iron and iron-based metals come into contact with a combination of oxygen and water. A chemical process takes place causing the iron element in the metal to oxidise, resulting in rust. If the metal is exposed to water that contains salt, i.e. in a coastal area or from road salt used in winter, the oxidisation process is quicker.
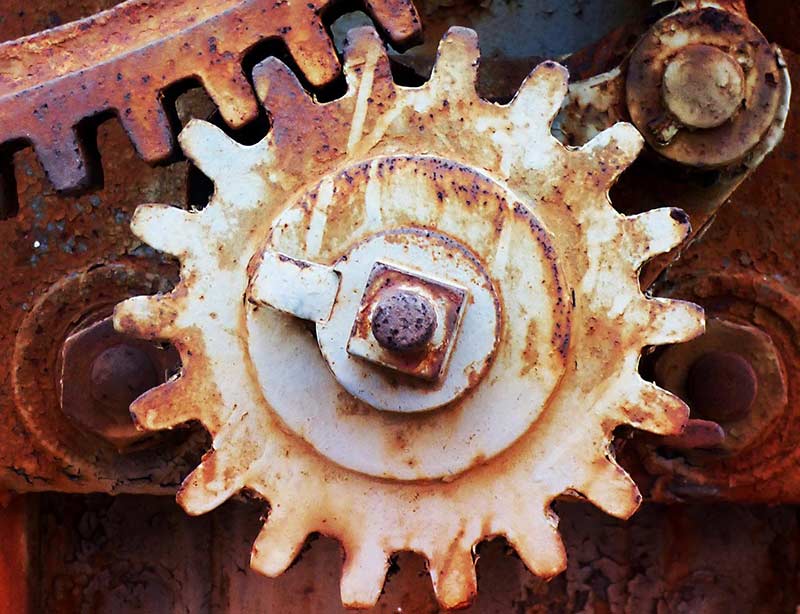
What is the rust removal process?
There are several ways to remove rust, some more time consuming than others. For small to medium-sized industrial equipment and tools, sandblasting or basic scrubbing can remove the rust, either by hand or using a mechanical device. However, for large industrial equipment, such as manufacturing machines, there are a variety of acid and water-based solutions that work well in removing rust. Depending on what you use and how much rust needs to be removed, there will be varying results.
The method you choose will depend on how much rust needs to be removed, the type of metal that is rusty, how many parts that need to be treated, and whether the treatment of the metal needs to take place 'in situ', such as large mechanical machinery, as well as the shape and size of the metal parts.
You will also need to consider:
- Safety of the area and the people carrying out the process
- How the rust removal solution you use will be disposed of
- How long the process will take, and the impact it will have on operations
To remove rust from machined parts, pipes and rebars, the following solutions and methods work well.
- Water-based solutions - one of the safest options is water-based solutions because they do not contain acid. It uses a different chemical reaction to remove the rust, and also doesn't damage the metal either. Water-based solutions can be brushed on the rusty metal, or the metal can be immersed into a rust removal bath - and through a chelation chemical process - rust molecules bond with the rust and lift it off the underlying metal into a layer of substrate. As well as being safe to use, it is also better for the environment in terms of disposal.
- Mechanical methods - the more traditional method is scrubbing or sandblasting the industrial equipment parts. However, it may not remove the rust as effectively, and it may leave an uneven surface which will result in not only a dull appearance but could also impact the way the equipment functions.
- Acids - often the more favoured option as it is fairly quick to do, and removes the rust effectively without damaging the metal. There are two types of acid-based solutions:
- Weak acids are not only safer to work with but are also less caustic and easier to dispose of. Weak acids, like EDTA, tannic, citric or oxalic acid, use a slightly different reaction to stronger acid-based solutions but are still effective. It must be remembered that just because they are weaker, they are still acid-based and can cause injuries. The advantage of weak acids in rust removal is that these acids are also found in the environment and naturally appear in fruit, vegetables and as additives in food and medicines. Therefore, they are far less toxic or caustic and easier to dispose of than strong acids. Because they are weaker, the chemical reaction process takes longer and is less volatile. They are available in gel form as well as suitable for rust removal baths.
- Strong acids and alkalis, such as hydrochloric acid, sulfuric and phosphoric acid, dissolve the rust through a chemical reaction process. However, they are very caustic - they will also react with other substances - and are dangerous to use, so they must be handled with extreme care and by a professional. This type of acid or alkali-based solution should only be used in severe cases of rust and by professionals in removing rust. They are highly corrosive, particularly if used in a concentrated form and not diluted, which is why they are usually available in a gel formation. It is important not to leave the strong acid sitting on the rust/metal for too long, or it could start to 'eat away' at the metal underneath and cause an uneven surface, called pitting. The other point to remember is that because they are so strong, the metal beneath becomes reactive and could lead to 'flash rusting'. So, the metal must be neutralised or sealed as soon as the rust has been removed. The correct safety precautions must be adhered to when using and disposing of strong acids, such as excellent ventilation, chemical resistant gloves and goggles.
- Electrolysis - this method also uses a chemical reaction process but is sped up by applying an electrical current. However, this is also a dangerous process and can emit toxic fumes and chemicals.
If you are looking to treat smaller items of industrial equipment that are rusty, make sure you follow the instructions for application, timings and disposal. If you're not sure, always consult professional rust removers. Using the correct method in the right way will remove rust effectively and bring industrial equipment back to life.
ESE Direct is a leading supplier of products for business, schools, colleges and universities, workshops and warehouses. With a wide and diverse range of products, more than 40 years of knowledge and experience in the industry, a bespoke design and installation service and exceptional customer service, you can trust ESE Direct.