We all love the look of a lovely, shiny metal product, even the humble garden bucket. But just how do you get that shine on metal? What makes it last for years? The answer lies in a process called galvanisation.
Many will have heard of galvanising or galvanised metal, but do you know what it is and what it means? Simply, it is coating a metal, like iron or steel, with molten zinc that protects the metal from rust, makes it more robust and adds that satisfying shine.
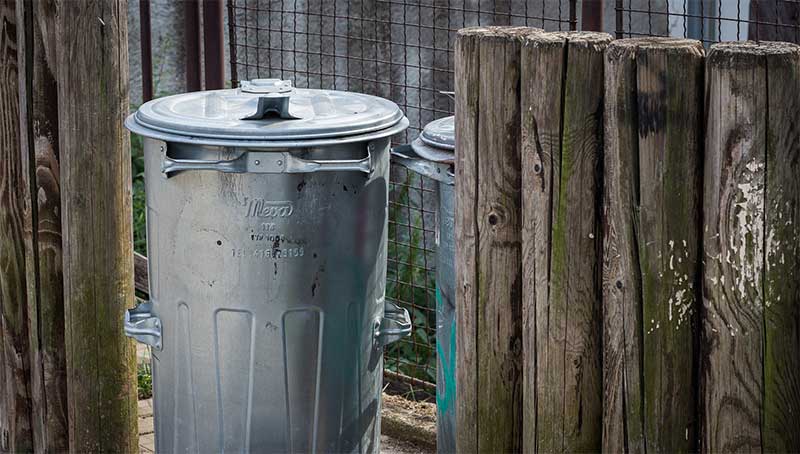
Think about the shiny metal items you may have seen in the last few days alone, from dustbins to trolleys and shelves to lockers and more. It's highly likely that they have all been galvanised. It might not sound like the most exciting subject, but there’s a lot more to galvanising metal than you might think. So, let's find out more about galvanisation, what it means, the process, why it's important and how it prolongs the lifespan of a product.
What is galvanising?
Galvanising, or galvanisation, is the method of applying steel or iron with a protective coating of zinc to stop it from rusting. But where did it originate? Well, it goes as far back as the 1780s and was discovered by Luigi Galvani. But it was Michael Faraday's work that coined the term galvanisation.
Galvanising metals started much later, in the 1830s, when a Frenchman called Sorel was granted the first patent for coating corrugated metal sheets with molten zinc. William Crawford took out a British patent for a similar process a year later. It is believed the first time galvanised corrugated iron was used was by the Navy at Pembroke Docks in Wales in 1844. The rest, they say, is history.
What does galvanised mean?
The galvanised coating is created through the metal and zinc reacting together, which leaves a smooth, often shiny protective zinc coating on the metal.
The thickness of the galvanising depends on the type of metal being coated and how thick it is, as well as how the final product is intended to be used (For example, a product used for heavy work will need a thicker galvanised coating). This is because different metals will react in different ways with zinc. It's also possible to create a thicker coating by grit blasting the surface of the metal prior to dipping it in the zinc.
What's the galvanising process?
So, how do you galvanise a metal? The most common method is immersing metal into a molten zinc bath at approximately 450°C (or 842°F!).
However, it must be cleaned before the metal is dipped into the zinc. The smoother the surface of the metal, the fewer marks or dull patches appear on the galvanised surface. The galvanising process produces a coating that is metallurgically bonded to the metal and creates a protective layer on the metal.
There are four main steps to the galvanising process:
- Cleaning - for the metallurgical reaction to occur, the surface of the metal must be completely clean; the better the preparation, the more successful the galvanisation, so there can't be any dirt, grease or other contamination. An alkaline or acid solution is used to degrease the metal, which is then rinsed with cold water. Next, it is dipped in hydrochloric acid at a room (ambient) temperature to remove any residual mill scale or rust and rinsed. In many cases, it is also recommended to use a fabricator to get rid of any other contaminations.
- Fluxing - the metal is dipped into a flux solution (around 30% zinc ammonium chloride at 65-80°C). This ensures any traces of oxide are removed and wets the steel for galvanisation.
- Galvanising - as described above, the thoroughly cleaned metal is dipped in the molten zinc, where the alloys of the metal react with those of the zinc and create a coating. This can take between four and six minutes, depending on the metal. When removed, as the metal cools, a bright, shiny surface appears.
- Post-treatment - the newly galvanised product can be treated further to prolong its lifespan using water or air cooling. Post-treatment is important to ensure a good quality galvanised surface; in many cases, a powder or paint coating can be added. In applications where the metal will be exposed to heavy external conditions, it can also be subjected to a chemical conversion coating or other more robust barriers.
How does galvanising affect the lifespan of a product?
Galvanising a metal is a cheaper option to protect the metal long-term from corrosion or rust. A galvanised metal can be recognised by what's called a 'spangle', which is a crystallised pattern found on the surface.
Galvanising significantly extends the lifespan of a product, particularly against external exposure. It ensures the metal is highly durable, protected against corrosion, and lasts many years. Indeed, galvanised metal can last for as long as 50 to 100 years if kept inside.
An added bonus is that iron and steel can be re-galvanised in the future, as long as it has been thoroughly cleaned and is free of contaminating elements. Steel, iron and zinc can also be recycled, making it an environmentally friendly, sustainable process.
Why is it important to galvanise metals?
Galvanising products like iron and steel, which are very prone to corrosion, is important to form a protective layer against the effects of oxygen and moisture. Galvanised metals are far more resistant to the weather's impact and are durable, robust and protected from damage.
Studies have shown that galvanising has a low environmental impact and is a sustainable method of protecting and re-using metals. It is a cost-effective way of producing longer-lasting products, too. The British ISO 1461 standard also ensures that the galvanisation process is maintained at a high level.
So, when you next buy a metal-based product such as a dustbin or shelving unit, opt for a galvanised product to ensure durability, robustness, sustainability, longevity and a nice shiny look!
ESE Direct have a wide range of galvanised products to suit almost any task, so look through our website. Can't find what you’re looking for? No problem - call us on 0808 258 0354 today, and our team will help you.