Online shopping accounts for 87% of all non-grocery retail purchases in the UK, according to Delivery Matters, a 2018 report by The Royal Mail.
This trend is creating a huge need for products to be picked and despatched. However, new companies selling online, often overlook their picking systems as they grow from operating in a spare room or garage to having their own warehouse.
Companies are expanding their ranges and offering increased customer choice, so it becoming ever more important that stock can be quickly and easily located. One often-overlooked way of increasing efficiency is to optimise the warehouse and implement an effective picking system.
Warehouse slotting is a popular way to organise stock in a storage space. This is the process where items are placed within a distribution centre in a way that maximises the space and reduces handling costs. Many logistic professionals consider this an essential component of a well-run warehouse.
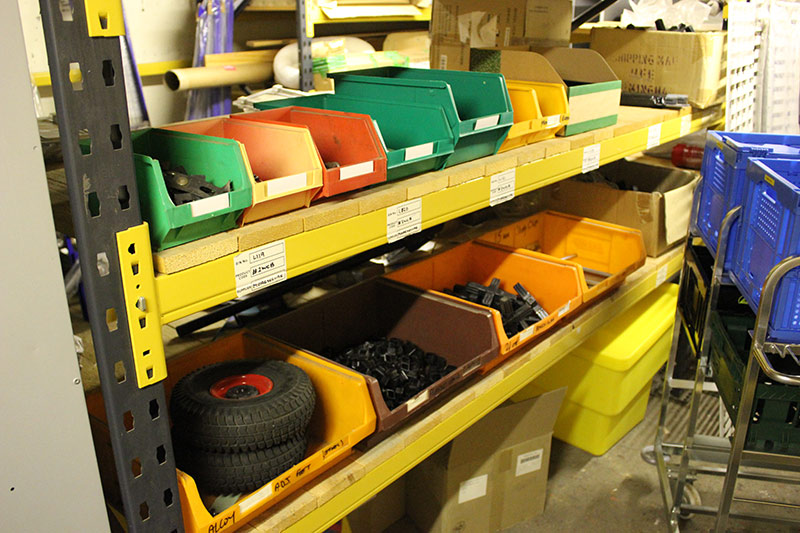
How do I get started with space optimising?
Although warehouse slotting is important, it is only part of a large warehouse design. The whole plan should encompass layout, racking design, management software and designated areas for packing and receiving goods.
Within this article we will explain the principles of effective picking and offer tips on how you can improve the process of selecting and despatching orders. We will cover the most important considerations and offer ideas to mitigate common problems and reduce picking errors.
Ecommerce giants, such as Amazon and Sports Direct, will have multi-million pound systems in place and often automate large parts of the process. However, there are still simple steps that small and medium sized operations can implement to create efficiencies in stock picking.
Why optimise bin locations?
The more efficient your warehouse, the more items can be found, picked and despatched within a day by each person. This keeps staff costs to a minimum and enables your company to make more profit or reinvest in other areas. The biggest single time-saving step will be to reduce the time spent walking between picking locations. This time can be reduced by 50% if you optimise key locations within a warehouse, group items and reduce the need to search for stock.
Picking accuracy will be greatly improved if stock storage is optimised, both in terms of location and visibility. This means that customers get the right products. Cost associated with returned goods can be very high. When less incorrect goods are despatched, profit will improve both in terms of customer retention and savings on returns and replacements.
What happens when a warehouse is poorly laid out?
When a warehouse is poorly laid out, staff may also fail to notice when items are getting low on stock. Stock is also replenished more efficiently when it’s stored in a well-organised system. Items will be less likely to run out or be overstocked. It's vital that workers can see items clearly so they can check stock levels easily.
Products will be assigned to the correct storage media when bin locations are optimized. Different parts of your warehouse could have different types of shelving or storage. Often different types of product are more suited to certain racking types because of variations in shape, size and weight.
When stock isn't properly located, it will also be at increased risk of damage during storage and packing.
Why is the correct storage system important?
Incorrect storage can lead to significant damage, for example valuable stock can be crushed when delicate items are placed in bins with heavy items on top.
Likewise, when expensive and vulnerable items are packed, the distance between storage and packing locations should be shortened This reduces the chance of stock getting dropped or falling off a trolley in transit.
Staff safety should be the prime consideration when stock is organised. The risks of injury associated with incorrectly lifting and moving items can be reduced by considering ergonomics and placing heavy items at the correct relative height to workers.
Now may be the time to revisit some basic first principles to maximising warehouse efficiency. Here we focus on 9 ways to improve picking operations.
1. Rank according to velocity and frequency.
In any business, it tends to be 20% of items that account for 80% of turnover. Once you understand which of your products are the most popular, it will help to position these so they are easily accessible.
As new items become more popular and old ones drop off, you can constantly monitor sales data to continually adapt as trends change. Seasonality will also play a part. For example, during the summer, garden furniture and toys will be more popular, so should be relocated during times when demand is high.
2. Group similar items together.
A great way to instinctively know where products are is to create common warehouse zones for families of products. This speeds up picking. Items can be categorised in any number of ways, from size, weight or fragility. Once grouped together, all the valuable stock can be securely locked away in one place, for example within lockable security cages.
A good example of this type of group organisation might be within a food warehouse. Individual areas for root vegetables, fruit, dairy and meat not only allows items to be easily located. It also means that each warehouse zone can be kept at the optimum temperature for its contents.
3. Keep as much stock as possible at ground level.
A lack of space can make it impractical to have all stock at ground level. Fast-moving products can be prioritised to racking and shelving at a convenient height. This will keep the process efficient.
Slower moving items can be placed up higher, as this reduces the need for steps to be manoeuvred, while still allowing available warehouse space to be utilised. This can still be used in conjunction with similar item groups. However, perhaps variants of the same product can share a bay, with the most popular size or colour at ground level and the other less popular ones higher up.
4. Reduce travel time.
The distance between popular products and the packing and despatch zone should be carefully thought out. Significant amounts of time can be spent travelling between bays even within a small warehouse. Even if items are physically close together, inefficient or badly planned walkways can still mean that time is wasted getting between locations.
Where items are often bought together, for example TV and associated leads, there should be an easy pathway between the two. Ideally items commonly purchased together would be located along a path that leads from the furthest item to the packing area without the need to double back or take an unnecessarily circuitous route.
Investment in conveyor belts will reduce travel time. These can do a portion of the walking for you by sending stock along pre-defined routes or straight to packing stations.
5. Set up hot zones.
A warehouse hot zone can be set up around the products that generate the most amount of picking activity. This means that travel time between different areas is reduced and staff can be concentrated where they are most needed. To minimise the time taken to complete each order these hot zones should be located as close as possible to the packing stations.
6. Choose appropriate storage media.
You wouldn't try to keep footballs on a shelf, just as you wouldn't store eggs lose in a pallet cage. Common sense usually dictates the right storage method for your stock, but getting it wrong can cause picking delays and damage products. Well-chosen storage media, where items can easily be replaced and removed will make order picking so much more pleasurable. Thought should be given to storage bins and the size of the opening on them so that staff don’t catch their hands or the products on inconvenient edges.
7. Maintain unique bin locations.
Similar items can be difficult to tell apart when picked under pressure, so it is better to keep to a system of a single bin for a single product. Imagine a system where you store three slightly different sizes of screw together in a bin, a large amount of time would be wasted trying to double check you had the right item. Three unique parts bins, each with clear labelling would significantly speed up picking and increase accuracy.
8. Make products visible.
Large open-topped storage bins or mesh pallet cages will make the contents of each picking location obvious so the correct products to be identified from a distance. Another advantage of keeping stock visible is that items that have been displaced and ended up in the wrong bin can be quickly identified and returned.
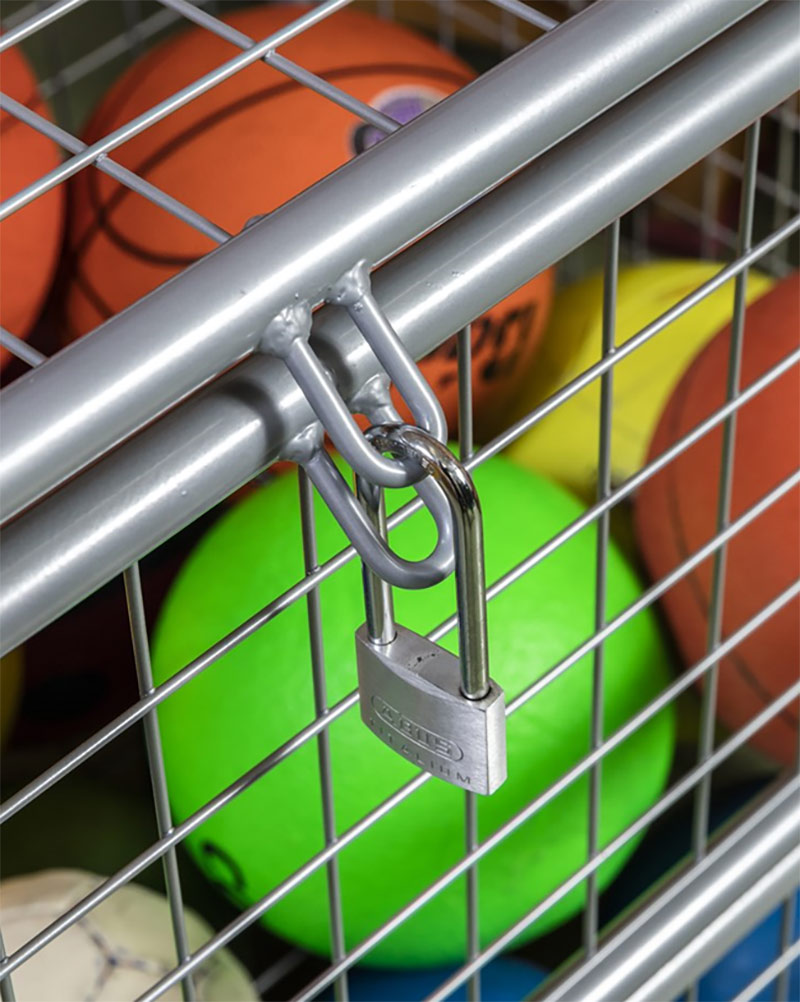
9. Prioritise ease of access.
The safest zone from an ergonomic point of view is between the chest and knees, picking items from this height is the quickest, most comfortable and least likely to result in injury. This means that fast-moving products should be placed within these area.
Workers who are forced to continually stretch or bend excessively during a working day are likely to make more mistakes and even have accidents.
If action is taken to eliminate even a handful of inefficiencies, this can greatly improve the picking success and therefore the profitability of any business.