The Government recently announced the implementation of 'Plan B' in the fight against Covid, with the requirement for people to work from home if they can. If the nature of your business involves staff working in a warehouse then it's likely that 'home-working' is simply impossible. It's one thing to move desks apart and manage an office environment where everyone is at their own desk, but how do you set up a functioning warehouse that keeps staff safe?
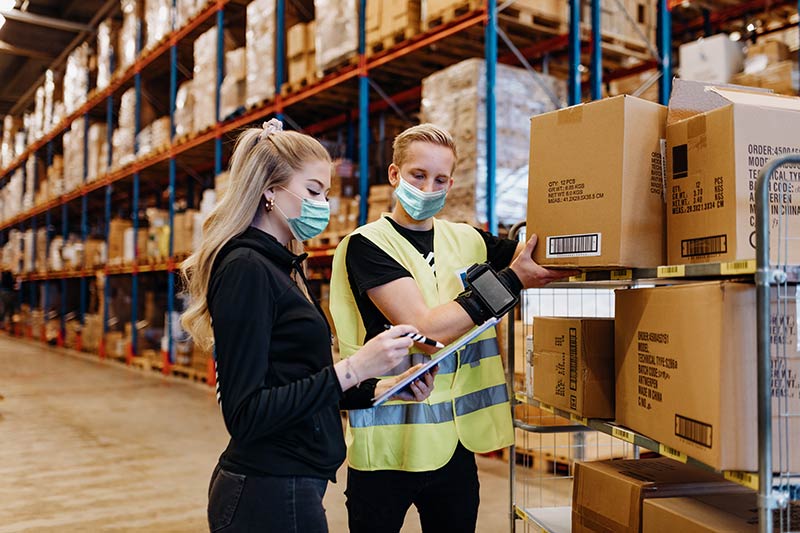
We first published some guidance back in November 2020 on how to set up a socially distanced and Covid-safe warehouse, and have re-visited the tips and ideas below. With some careful thought and attention, by making signage clear and giving everyone clear and unambiguous instructions it should be possible to ensure your staff can all work safely:
Place sanitisers at entrance points
Hand sanitising stations are most effective when they are the first thing people do when they arrive at work, prior to touching anything. This means placing dispensers at each entrance. For reduced contamination, these should be either via an automatic sanitiser dispenser station or automatic sanitiser dispensers, reducing the need for multiple people to touch the same points. Encourage staff to use sanitiser regularly, especially if they are moving between different warehouses or zones. Ensure there is an adequate supply of cleansing liquid and that someone is responsible for keeping dispensers filled. You can also issue staff with their own small bottles of hand cleanser to use whilst on the go.
Set up a temperature testing area
A good way to spot potential symptoms early is to set up daily temperature checks for staff and visitors. Although there are many reasons for someone to have an elevated temperature, it could be an indication that they should get a Covid test. Temperatures should be taken with a non-contact infrared thermometer, by a person wearing the appropriate protective equipment, such as a high filtration face mask or face shield. This is because they may need to get quite close in order to take an accurate temperature.
Regularly clean touch points of trolleys or handling equipment
Unless you are in a position to assign each warehouse worker with their own picking trolley, there is going to be significant sharing of manual handling equipment. Anti-bacterial wipes should be supplied so that equipment can be wiped down after each use. This should also apply to any shared computers or phones.
Assign the minimum of people to each picking area
If practical, assigning a single person to each area of a warehouse will reduce the risk of people getting too close to each other and reduce the amount of common touch points. If this isn’t possible, assign groups of people to picking areas and discourage staff from going into zones that they are not assigned to.
Install hygiene screens at packing stations where room is limited
There will be situations where due to the need to have access to a desk or machinery, it will not be possible to maintain a two metre distance. This could happen at common packing points, where good come to before final dispatch. Either think about erecting clear plastic screens between marked out work areas or provide masks or face shields. If there are zones where you do not want people to stand, clearly mark these with floor tape or appropriate signage.
Mark out one-way systems through common areas
Warehouses can have narrow walkways and bottlenecks caused by doorways, reduce the chances of people needing to pass close to each other by marking out one way systems that keep opposing traffic apart.
Limit numbers in kitchens and toilets
Social distancing whilst people are working isn’t going to be very effective if everyone heads to the same small canteen at lunch time or tries to use the toilet at the same time. Remove tables and chairs to prevent gathering and attempt to implement a system that allows people to know when the toilet is free. This could be via a queue management traffic light system or by wedging open external bathroom doors (where appropriate).
Stagger start and finish times
You can reduce crowd at door ways or in car parks by simply allowing people to start and finish shifts at ten minute intervals. This could be particularly effective if there is a need to change clothes after work, reducing the amount of people in changing areas at any one time.
Limit the number of external visitors
No one is suggesting that vital repairs or safety inspections are cancelled, but it is worth considering if things like training could be done remotely or if a forklift could be serviced outside instead of bringing an external engineer into your warehouse. Assess each potential visit on its own merits and decide if it needs to be done, if it can be done at a distance or how it can be most safely achieved.